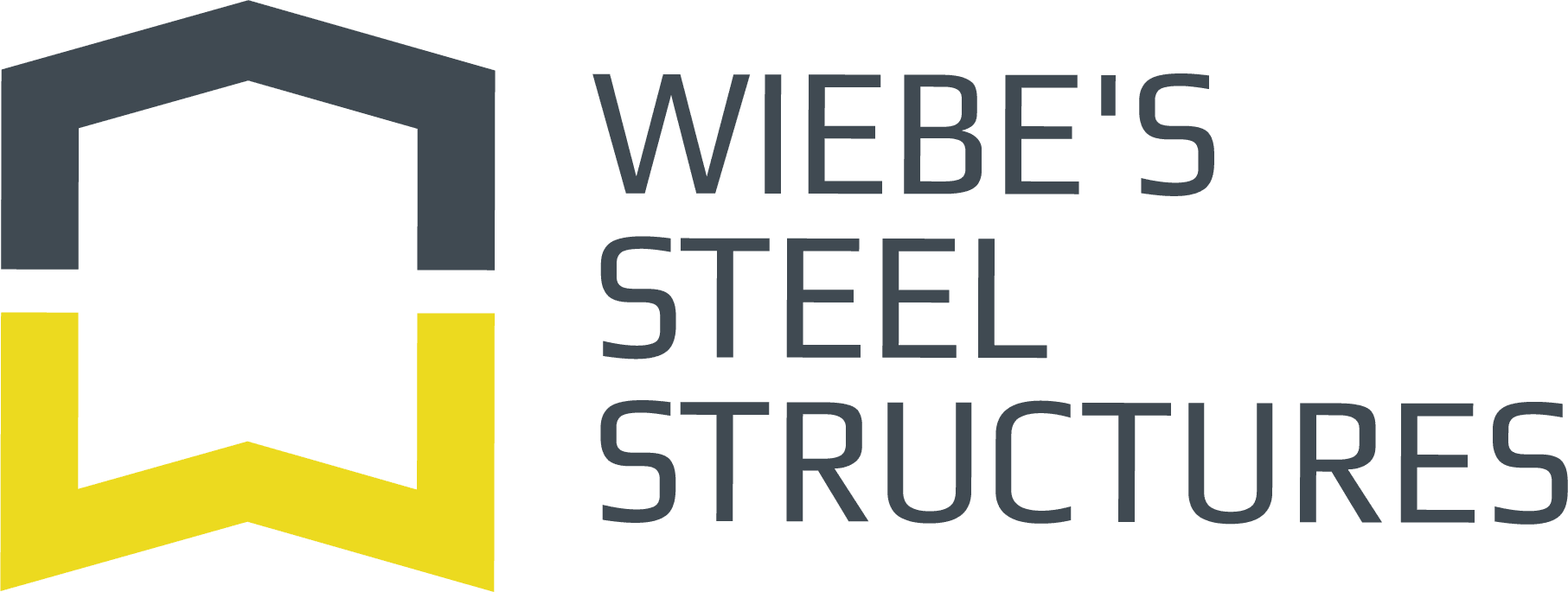
From Chaos to Clarity: How Wiebe’s Standardized and Scaled with Ontraccr
Wiebe’s Steel Structures turned to Ontraccr to bring structure to their growing operations. By consolidating workflows and improving visibility, the team was able to simplify budget tracking, reduce administrative overhead, and better coordinate project delivery. The platform’s flexibility allowed them to build processes tailored to their needs, helping the company scale without adding unnecessary complexity.
☻
Operational Efficiency
⛮
Integrated Workflows
↑
Enhanced Transparency
Standardized data gives teams clear visibility into project status and financials.
Company
Wiebe's Steel Structures specializes in steel construction and project management services across Canada, with expanding operations notably in Alberta.
Industry/Services:
Number of Employees:
Background:
Wiebe’s Steel Structures, a growing company specializing in pre-engineered steel building construction, faced a challenge common to many expanding companies: their workflows didn’t scale. Each project manager had their own system: spreadsheets, personal checklists, and ad hoc documentation. This made it nearly impossible to train new employees or maintain consistent execution across the team. While this approach worked in the early days, it became increasingly difficult to maintain visibility and standardization as the business grew.
The lack of unified workflows affected not just operations, but also financial oversight. Budget tracking was fragmented, and there was no reliable way to monitor expenses or margins in real time. Leadership saw the risk. Without a centralized, standardized system, growth would lead to chaos. That’s when the search for a solution began.
Solution:
Wiebe’s Steel Structures began looking for a digital platform that could help them standardize and scale their operations. After researching and testing several options, including Procore, Contractor Foreman, and Viewpoint, they found that Ontraccr offered the best combination of flexibility and ease of use. The platform allowed them to set up custom workflows that reflected the way they actually worked, without needing any coding or complex setup. The team quickly aligned around Ontraccr as the best fit for both their current needs and long-term growth.

“Ontraccr has definitely saved us a lot of time on admin work and made everything easier to access. Having budgets and documents all in one place has streamlined a lot of what used to be scattered.”
— Maik Friesen, Wiebe's Steel Structures

Implementation Process
Wiebe’s took a practical, step-by-step approach to implementation. Instead of waiting for the entire system to be set up, the team began testing features immediately. They built workflows incrementally and reached out to the Ontraccr support team whenever they needed help.
They started with core tools like project profiles and budget tracking. Once those were working smoothly, they added invoicing, digital boards, and later integrated QuickBooks. This gradual rollout helped the team avoid overwhelm and ensured each feature was properly adopted.
Workflow Implementation and Key Processes
With Ontraccr, Wiebe’s Steel Structures moved from fragmented manual systems to a unified digital environment. This shift brought consistency and visibility across all teams, allowing operations to scale without sacrificing efficiency or accuracy.
- Integrated Boards Across Departments. Beyond individual workflows like budgeting and quoting, Wiebe’s built a network of interconnected boards tailored to various departments. These include dedicated boards for estimates, change orders, project tracking, scheduled jobs, HR/staffing, and even marketing initiatives. Each board is connected through shared forms and data inputs, creating a unified operational system that reflects the full scope of their business.
- Budget Tracking. Previously, each project manager used a different approach, from spreadsheets to handwritten notes, which made it difficult to maintain oversight. Now, all budget data is centralized, giving both financial admins and PMs a shared, accurate view. This reduced duplicate work and made reporting faster and more reliable.
- Lead-to-Quote Workflow. Before Ontraccr, proposals were written manually in Microsoft Word, often requiring repeated revisions and copy-pasting from emails. Now, using dynamic forms with built-in logic, the team can generate branded PDFs in minutes. This streamlined process saves hours each week and reduces confusion, especially with repeat jobs or recurring scopes.
- Project Documentation. The team replaced scattered paperwork with digital forms and customizable PDF templates, covering everything from checklists to field updates. This improved coordination and ensured records were accessible during audits or handoffs.
- QuickBooks Integration. Connecting Ontraccr to QuickBooks reduced manual data entry and improved the accuracy of financial tracking. With real-time sync between the field and the office, project profitability became easier to measure and manage.
Results
Implementing Ontraccr delivered noticeable time savings and streamlined work across departments. Tasks that previously took several hours were often reduced to under 15 minutes. Project managers no longer had to verify budget figures manually or chase down files. Instead, they could focus more on execution than administration.
These time savings were amplified by the interconnected nature of Wiebe’s workflows. Instead of juggling separate tools for estimating, HR, project scheduling, or daily reporting, all activities now live within one platform. This cohesion not only improved operational visibility but also made it easier for teams to collaborate and adapt as the company scaled.
Crucially, the standardized workflows and shared access to data improved coordination across teams and regions. The team found it easier to keep everyone aligned, which reduced miscommunication and duplicate efforts. In some cases, the efficiencies gained made it possible to avoid hiring additional staff. This helped the company grow without increasing overhead.
Future Outlook and Expansion Plans
Wiebe’s Steel Structures continues to prioritize digital growth as they expand into new regions. With a new office in Alberta, the team is implementing Ontraccr’s Divisions feature to organize projects by location while maintaining company-wide visibility. This setup improves reporting accuracy and gives regional leads better control over their data.
They are also exploring automation opportunities through Zapier, aiming to connect Ontraccr with other tools already in use. These automations include streamlining client onboarding and syncing schedules with calendar platforms.
Looking ahead, the company plans to take full advantage of Ontraccr’s analytics and time-tracking tools. These features will help identify productivity patterns, uncover inefficiencies, and inform smarter staffing decisions. They are also building on their board system to bring even more operations into Ontraccr. New use cases like purchase order tracking, daily summary logs, and field material intake are already live. This expansion reflects their goal to create a single digital hub for every department.
Over the long term, Wiebe’s is excited about Ontraccr’s product roadmap. New features like AI-driven assistants and real-time workflow suggestions will enable the team to optimize proactively. With each enhancement, they are building toward their vision of a fully digital company where all critical operations — from estimating and compliance to scheduling and billing — are managed through one adaptable platform.