Simply just having a safety program is not enough to ensure that it is successful. It requires the right elements and focus to be effective. Safety programs are most successful when they are well-defined, supported by leadership and management, and continually improved.
The program should be led by top level management, who must be committed to its success. It is based on a team effort involving employees at all levels of the organization and it allows employees to understand their individual roles and responsibilities in order to achieve common goals that company leaders evaluate on an ongoing basis.
Below I've highlighted 5 key elements that need to be in place in order to ensure the success of your safety program.
1. The Culture - Employee Training and Empowerment
Before employees are expected to follow best practices, it’s essential that you educate and empower them to hold each other accountable. This can be done by dedicating a day to safety training where you share safety tips and plan activities that keep your workers interested. Online resources should be used as they can provide safety training ideas with minimal effort.
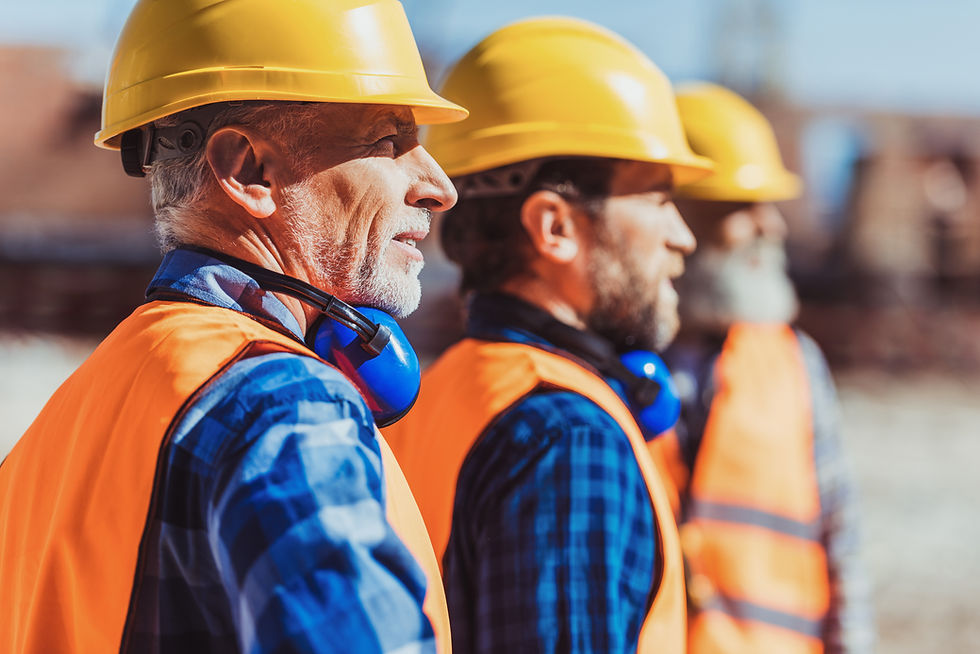
To boost accountability, consider implementing a stop-work authority, which gives employees the power to stop a task if it becomes too risky for them or their co-workers. If you want to sustain your culture of accountability throughout your organization for years to come, putting safety in the hands of your workers can help you foster accountability at all levels of your company.
2. Systems for Hazard Identification & Control
The first step in controlling hazards is to identify them. A safety management process must be put in place for workers to easily identify hazards and take appropriate steps to contain them. Not all hazards can be eliminated, but most can be controlled; this is the goal of your safety program.
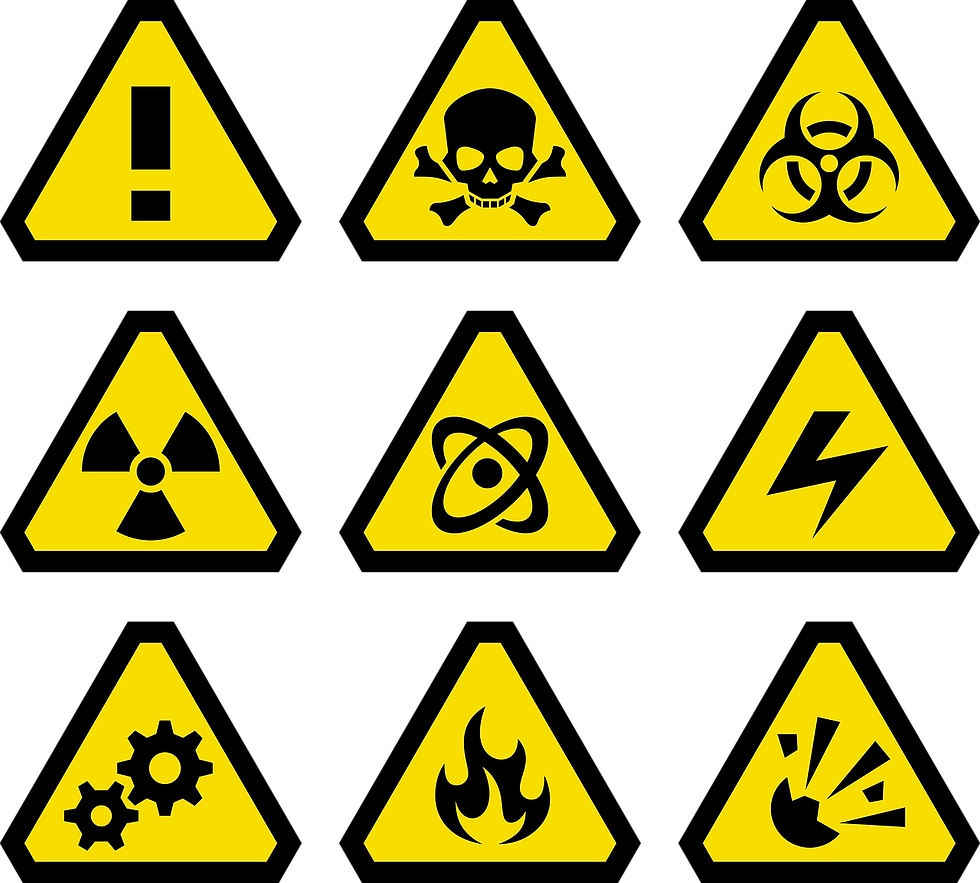
Control hazards through a combination of methods: physical controls (barriers, guards), administrative controls (procedures), and personal protective equipment (PPE). Physical controls should always be your first line of defense against any potential injury or health risk. Institutionalize these into your overall procedures by integrating them into regular work processes so they become second nature for everyone on the team.
Use administrative controls whenever possible, like scheduling certain jobs when it's not busy so fewer people are exposed to risks at once—this also helps with communication across teams! If you're working with hazardous materials offsite or overseas then PPE is certainly necessary—just make sure it's reliable enough that no one gets hurt while wearing it!
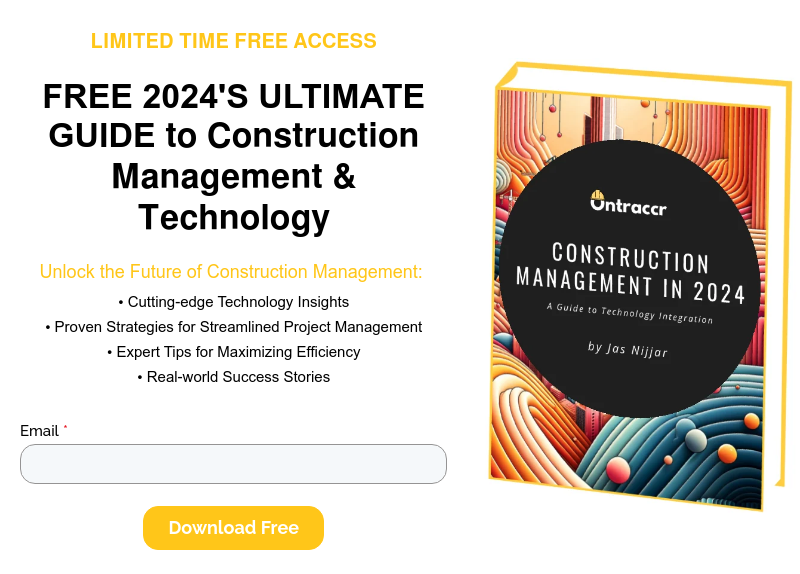
Verify that all these measures are effective by conducting regular inspections throughout every aspect of each process being monitored. This not only ensures that everything stays up-to-date but it also gives people confidence knowing their work environment has been thoroughly assessed before being put into practice.
3. Emphasis on Compliance
Compliance with laws and regulations is the most obvious way to ensure a safe work environment.
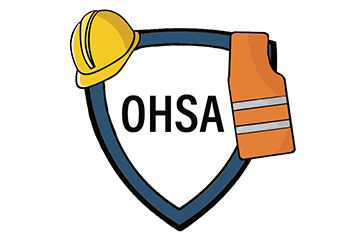
Along with government agencies like OSHA and ANSI (the American National Standards Institute), companies should develop their own internal best practices that they can use to outline specific job-related safety procedures. For example, if you’re involved in construction projects, there are several standards that apply: OSHA 1910 Subpart N (Construction) governs fall protection requirements for scaffolds; ANSI A10 as well as ANSI D16 promote best practices for proper ladder selection; and OSHA 1926 Subpart L prohibits workers from carrying more than 50 pounds when operating a scissor lift or aerial platform unless two safety lines are attached by two separate means of attachment.
By creating formalized policies that outline these best practices and make them easily accessible to all employees, you can help ensure compliance across the board.
4. Strong Leadership & Organizational Buy-In
It's not enough to write a safety program, implement it and expect it to work. You need strong leadership and organizational buy-in in order for your program to succeed. This means that everyone from the CEO or owner down through every level of management needs to be committed to the success of your program.
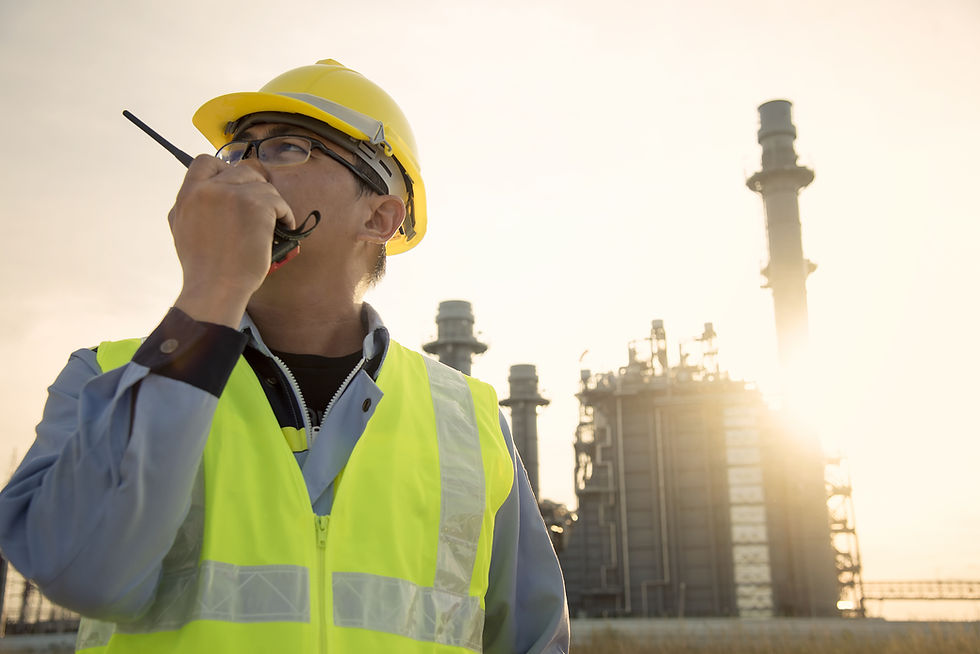
Strong leadership is key here; good leaders motivate their teams with clear direction and set high but attainable standards for them to achieve. They also communicate consistently about issues such as deadlines, quality control and other critical areas related to their organization’s success or failure during difficult times. And they do this even when no one is watching. Strong leaders always set an example for others by practicing what they preach!
Set high but attainable standards for them so that everyone understands what is expected of them according to strong leadership principles like accountability, cooperation, consistency/predictability, fairness (being fair even when making tough decisions), and flexibility/adaptability.
5. Continuous Improvement
Continuous improvement is about making small, incremental changes over time. It’s not about doing things faster or more efficiently; it’s about being better at what you do every day.
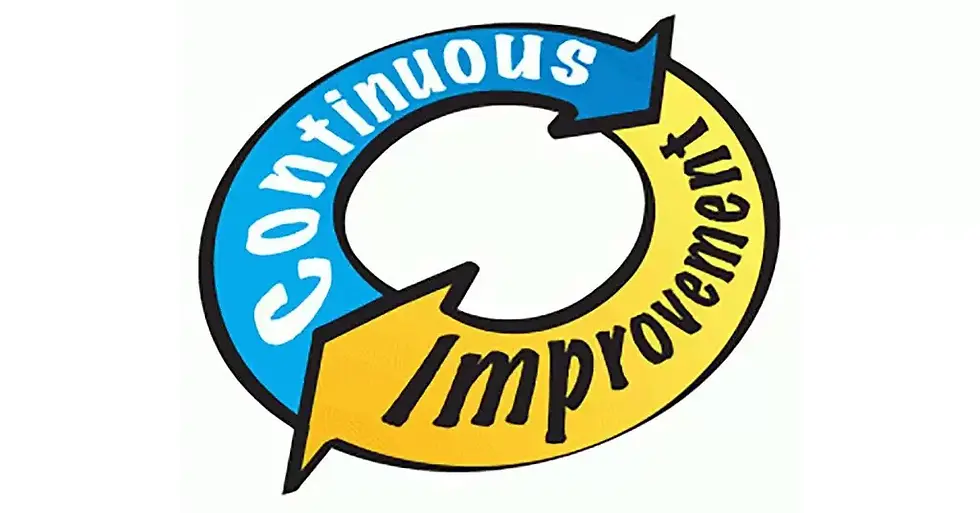
Continuous improvement is a mindset that can be adopted by anyone—no matter your role or experience level within the organization. You just need to have an open mind and accept that good enough never really is good enough, and that there’s always room for improvement. Small changes add up over time, so set aside some time each week (or even every day) to evaluate how things are going in your safety program and make adjustments accordingly.
If you hold frequent safety meetings with your team members, consider retraining them throughout their tenure with the company as regulations continue changing (especially if they have been around for a while). This will ensure they remain up-to-date on industry standards while also keeping everyone engaged in an ongoing discussion regarding best practices within your organization's culture of continuous improvement.
The Role of the Safety Manager
The safety manager is responsible for overseeing all aspects of the safety program. This person ensures that their staff have access to information related to health and safety, as well as training in how best to minimize or avoid risks at work. They are also the point of contact for all matters related to health and safety within your organization, so it's important that you choose someone who can perform this role effectively.
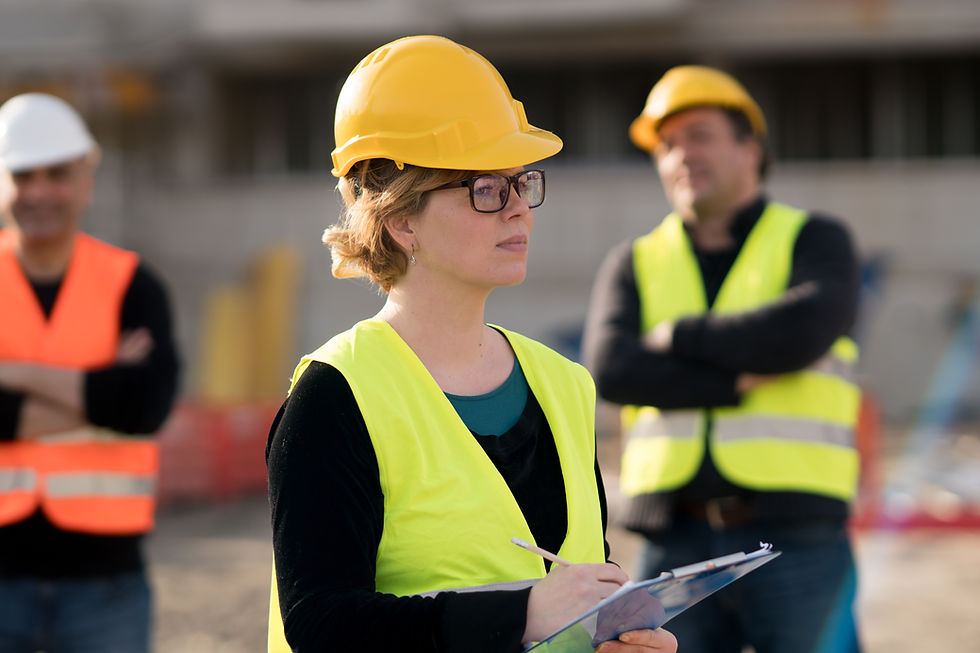
The responsibilities associated with being a good safety manager can vary depending on your industry or workplace size, but they should include:
-
Identifying and monitoring health and safety hazards within the workplace
-
Training employees on how best to avoid injuries while performing their jobs
-
Reviewing legislation related to health and safety standards; ensuring compliance with these standards where necessary
-
Performing regular inspections of the workplace environment
-
Writing policies specific to your organization's needs (for example: "Effective Safe Work Practices", "Fire Prevention Policy")
In addition, you will want them performing various administrative tasks such as coordinating emergency drills with other departments/employees so everyone knows what actions need to be taken during an emergency situation.
Conclusion
I hope that this article has helped you understand the importance of having a safety program in place. Safety is not just something that affects your workers—it affects everyone, including customers, employees and your bottom line. A good safety program will help protect you from potential lawsuits and fines while also keeping everyone safe on the job.