In the construction industry, the supply chain is the heart of any project. Without it, you can’t build anything as it’s the foundation upon which all projects are built and maintained.
The good news is that this aspect of your operations has been honed to a science for decades—but what about disruptions? Do you know what it takes to maintain a strong supply chain during these times? And if something goes wrong with your supply chain, how do you respond effectively? Here's how:
Plan ahead
The best way to combat supply chain disruption is to plan ahead. If you know what you’re dependent on, and what the risks are to those dependencies, it's easier to identify alternatives or solutions. This won't prevent the disruption from happening in the first place, but it will make it easier for you to recover quickly once it has happened.
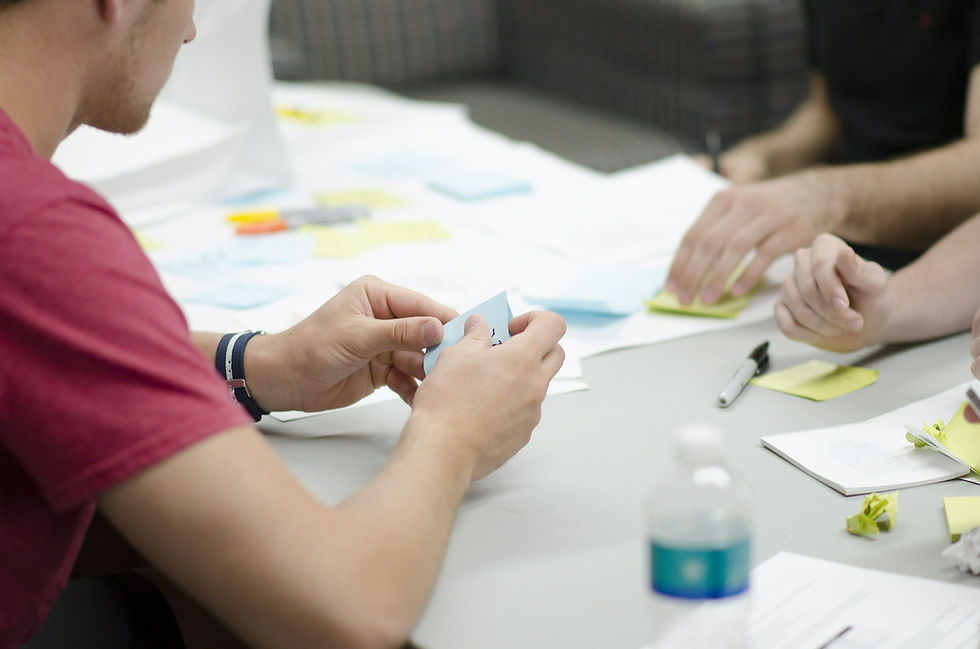
Planning ahead means doing some research into your suppliers—not just who they are and how much they cost (though those things are important too), but also how reliable they are at shipping products on time and within budget. Check with them before approaching clients about using their materials and products because this will help you identify any potential risks or issues that may arise when they do not meet an agreed-upon deadline or budget.
Planning ahead also means identifying alternatives—what other materials could work instead? And if nothing else works, what resources do we have access to outside of our current network? Having this kind of mindset can also help identify potential opportunities as well as threats.
For example, you may stumble upon a new supplier or material that is more cost effective and takes way less time to install than what was proposed. On the flip side, you may discover through your careful interview process that the proposed supplier has a long track record of missed deadlines and budget overrun, allowing you to steer clear of a potential delay.
Don’t put all your eggs in one basket
The importance of diversity in supply chains is well known within the construction industry. However, it’s not always easy to know how best to achieve diversity. Below we'll discuss some of the factors that should be considered when planning a supply chain strategy and provide some tips on how to manage risks more effectively.
One of the first things you should do is consider where your materials are sourced from and check what suppliers are available locally or further afield. For example, if you have a project across Sacramento or several other major cities in the US, then sourcing from different locations may suit your needs better than sourcing everything from one place only (which would mean extra transportation costs).

It’s also worth thinking about whether all products used must originate from one supplier - for example, if there's an issue with a specific manufacturer or product line, could there be alternatives available? Or perhaps another supplier could develop alternative products which might work just as well but prove less risky overall because they're not made by such an unreliable source?
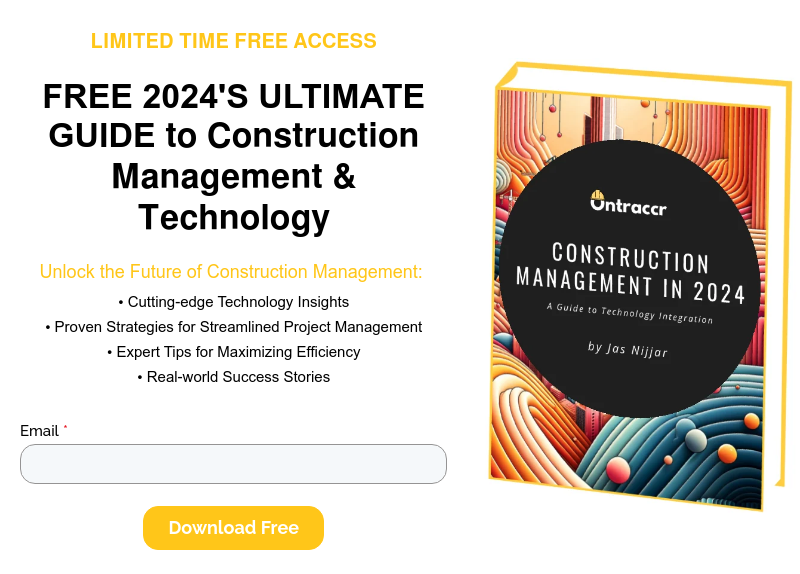
Finally, you should think about how your suppliers will manage the risk of their own supply chain. They may have certain policies in place that help them avoid potential issues such as price increases or delays to goods but these won't be effective if they're not communicated properly to other parties who need to know about them. If your supplier has a policy in place then this should be clearly outlined so everyone can understand exactly what's expected of them in the event of any kind of disruption.
Find alternative suppliers or alternative products & materials
If you can't find an alternative of the same quality and price, consider an alternative product or material.
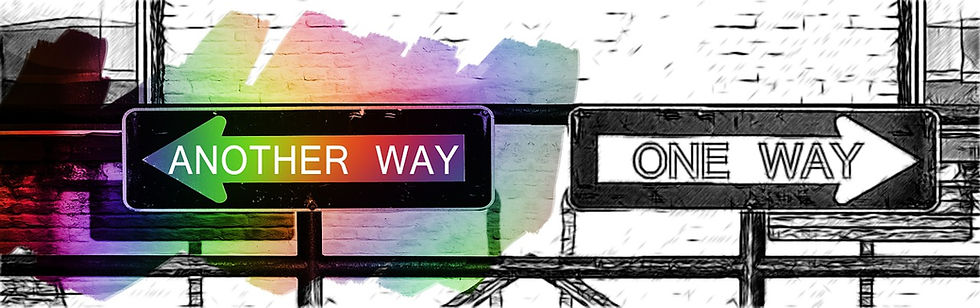
For example, if your supplier doesn't have the right size of cable for a job, look for something similar that will work instead. If there isn't an equivalent product or material available then try to create one yourself! This will take time and effort but can be worth it in the long run if you're trying to save money on construction projects.
Of course this isn't always possible, but there may even be a chance for you to design the required item yourself and have a local manufacturer make it for you. I've personally done this in the past with the back-boxes for EV chargers, and the result was a solution that was cheaper and better quality than what the original manufacturer could provide!
You should also talk directly with your suppliers about their experiences dealing with supply chain disruptions so they can help you avoid any future issues as well as provide advice on how best to deal with them when they occur.
Make local and domestic supply a priority
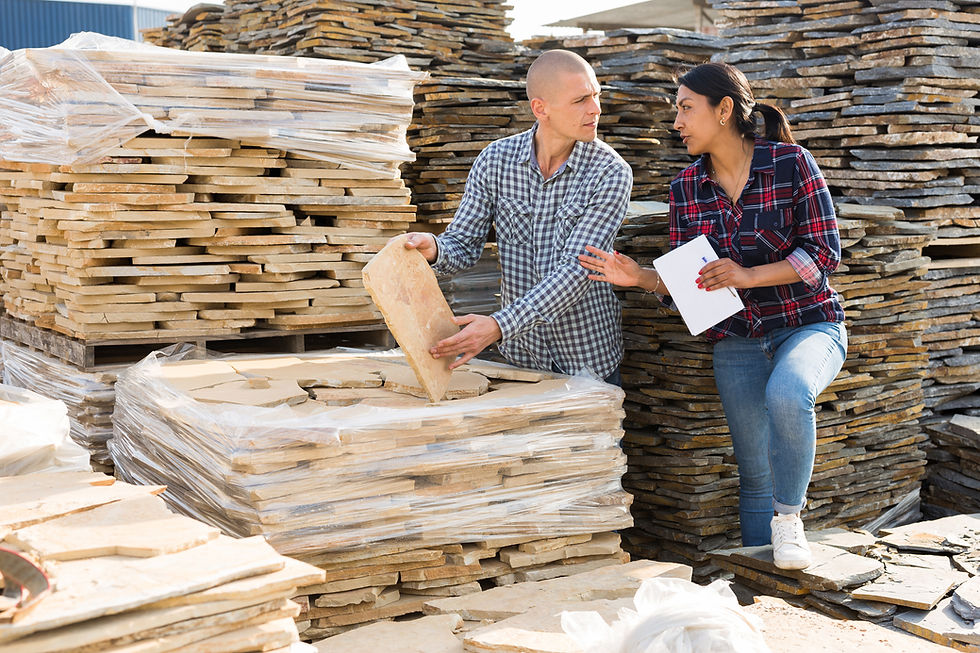
Another important step in mitigating supply chain disruption is to make local and domestic supply a priority. We’ve talked about the importance of buying local before, but it bears repeating: purchasing material from local suppliers reduces your risk, promotes the local economy, and can have a significant environmental impact by eliminating the resources required to transport that material across great distances.
Another benefit of buying local is that it can contribute to job creation within your community—in fact, some research suggests that supporting small businesses in your area could lead to up to seven times as many jobs per dollar spent than shopping at big box stores like Home Depot or Amazon.
Consider repurposing or recycling
One of the best ways to combat supply chain disruption is to repurpose or recycle. Not only will this save you money, it'll also be more economical and help the environment. Using recycled materials can take less energy, which means that you'll be saving even more money than you would if you were just using new materials.
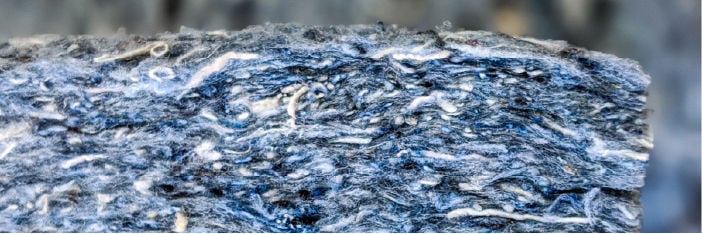
Consider using materials that can be repurposed or save excess material for other applications. This way, when it comes time for repairs or maintenance work on your project, there won't be any need to buy new material because you'll likely have everything you need in your warehouse! Finally, reusing existing materials will save both time and labor costs down the line—and who wouldn't want that?
Having a strong supply chain is integral to construction project success—including being prepared for disruption
Your supply chain is the backbone of your business, so you need to make sure that it's strong. As a construction manager, you may have a ton on your plate—but don't forget about the importance of keeping track of your suppliers and making sure they're reliable.
-
Build strong relationships with suppliers: Building strong relationships with vendors isn't just about getting them to give you discounts or special treatment. A good supplier should also be interested in helping you plan ahead for potential disruptions in the supply chain and ensuring that everyone knows what their role is during those times.
-
Be prepared for disruption: Don't wait until something goes wrong before having an emergency plan for dealing with supply chain disruptions (like when construction materials become unavailable because there's been a natural disaster). Have an alternate channel in place so that any necessary changes can be made quickly without disrupting schedules or causing delays on other parts of the project as well as other projects being worked on at different sites simultaneously.
-
Don't put all your eggs into one basket: If possible, break down larger orders into several smaller ones so that if one shipment doesn’t arrive due to weather issues or road closures due to accidents caused by bad weather conditions such as snowstorms then there will still be enough material available overall for work to continue.
While supply chain disruption may seem like an inevitable part of business, there are ways to overcome it. By planning ahead and being flexible, you can avoid delays and keep your projects on schedule.