No two jobs are the same in construction, which makes estimating tough. One of the most crucial ways you can improve your future estimates and to increase your profitability is to organize them through the use of cost codes.
What is Job Costing and how does it help?
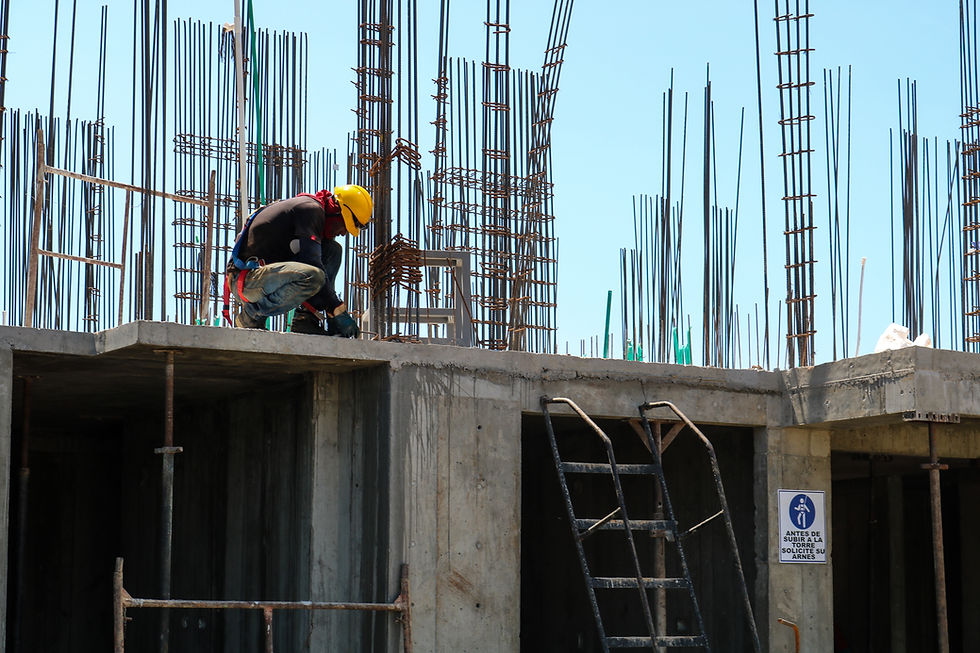
Simply put, Job costing is a widely used construction accounting system that breaks down a project into smaller and more specific tasks. Typically in construction this is done through the use of cost codes, which represent common tasks that your workers would perform on the job site.
With the use of the following methods, you will be able to calculate the actual costs of working on construction projects, and ultimately make more accurate estimates. This in turn means you’ll be able to assign a detailed budget to a project, and track progress on each of those specific cost codes, which further unlocks the ability to make smarter business decisions and avoid costly labour over-run.
1. Break Down Your Project Into Phases & Cost Codes
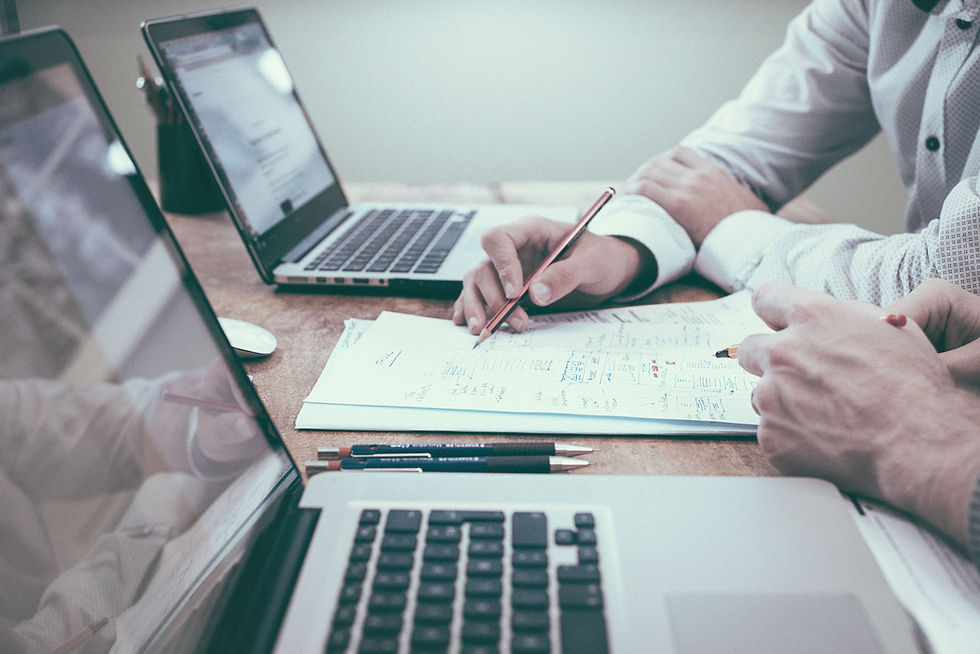
The first step to job costing is arguably the most important as it organizes your project into smaller and more measurable chunks. This is done with the use of phases and cost codes, which are essentially the building blocks of job costing.
Often times contractors may use a reference called the Master Format to help them come up with these cost codes, but this format is typically intended to help organize project documents such as scope of work. As a result it often will lack a lot of additional cost codes that your organization would see serious benefits from tracking, especially those related to indirect labour, such as supervision, quality control, and design work. Therefore we recommend that the Master Format be used as a good starting point, while keeping in mind that further refinement will be needed to ensure all aspects of your business are covered.
-
Start with each main phase in your project. For example, a 6 storey apartment complex can be broken down by each level, which would represent a phase (i.e. Level 1, Level 2, Level 3, Level 4, Level 5, and Level 6). This is important because it allows you to break the project down into smaller chunks which you can then monitor more accurately for productivity.
-
Then within each of these phases, you can further break the project down into the specific tasks or cost codes. These are usually unique for each type of construction company, but once you have a list of these cost codes it is best to standardize them throughout your projects as they don’t typically change too often. The level of detail that each code represents will vary and is typically based on how large an organization is. Examples of cost codes include framing, drywall installation, electrical rough-in, and finishing work.
-
Finally, once you have the list of phases, and cost codes, you can further organize this list by categorizing them into one of the three categories: labour, material, and overhead.
Labour
As a construction contractor, you should have a clear idea of how much direct & indirect labour is required to complete your project.
Direct labour represents the hours that are directly required to complete the project. You can think of this as the hours needed to finish a specific task and are directly involved in the active conversion of materials into finished products.
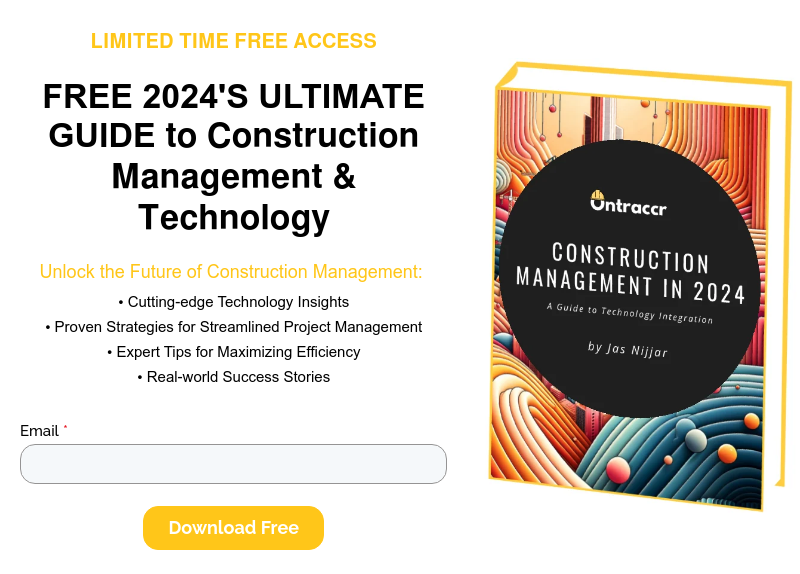
Indirect labour represents the hours that are required to support the production process. These hours aren’t directly involved in the conversion of materials into finished products. An example of indirect labour would be supervision hours which typically represent the time of a supervisor, foreman, project manager, or designer.
Material
Much like labour, material can also be further broken down into direct and indirect. Direct material would be material that is being installed in the project as part of the finished product. Indirect material represents things like the rental of machinery or tools required to aid in the construction of the finished product.
Overhead
Caution! - This is where a lot of companies seem to miss the boat. There are more costs associated with a project than simply labour and material. Your company may require a project manager to manage the project, or perhaps you have to pay rent for your office/warehouse. All indirect costs should be taken into account when estimating a project, especially if the job requires extra overhead to manage it.
2. Gain an Advantage by Investing in a Good Software Solution
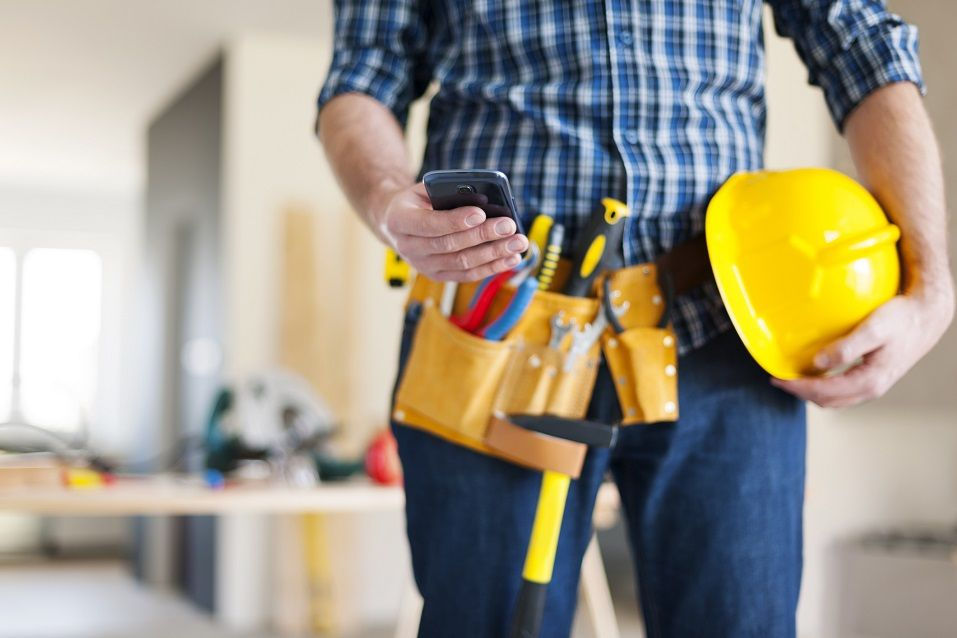
Job costing can be a lot of work, and typically requires more overhead to implement and maintain within your company. For this reason, smaller contractors often are turned off from the idea of having to implement such a system within their organization. Fortunately, technology has become more and more prevalent in the industry and there are several software options that you can use to help automate a lot of the hard work.
So how do you know which solution is right for you?
Two of the biggest factors in evaluating the right software solution are usability and cost. Unfortunately for the industry, a lot of the software solutions that have been available over the last couple of decades have not truly achieved either of these two important factors. This makes them unsuitable for small to mid-size contractors who can't afford or are unwilling to support the overhead required to introduce them.
If the software is not so easy to use, not only will you be frustrated, but so will your team. When your team doesn't buy-in to the use of the solution, you just end up paying a ton of money for a solution that is not providing you any value due to its limited adoption throughout your organization. That's a pretty bad deal, right?
This is where Ontraccr comes in. Ontraccr is extremely easy to use, requires next to no training for your staff, and is highly affordable, making it a great solution for organizations of any size.
With the use of a field management software like Ontraccr, you can quickly standardize these job costing methods and have them run on auto-pilot. Some of the main benefits of software like this include the ability to view and track labour spend in real time, forecast labour over-runs, and ensure cost codes are within budgets. Lastly, they create an easy to navigate interface for all members of the organization, from managers in the office down to field workers at the job site.
This is key for getting buy-in from your employees as it greatly reduces the overhead required to maintain the incredibly beneficial job costing system.
3. Review Job Costing Reports Regularly
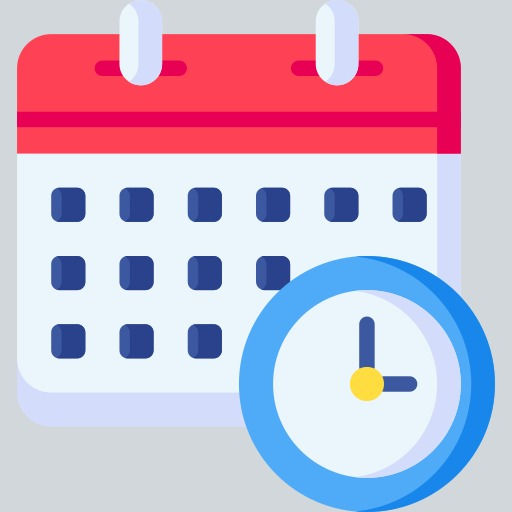
The last step to successfully transforming your organization to one that is a lean mean job costing machine is to ensure that you are regularly monitoring and reviewing reports generated by your job costing software.
This can help quickly identify any areas of work that are in the red, or on the flip side, where profits are expected to be better. Staying on top of this throughout the duration of the project will help you identify any issues before they become full blown problems.
There is nothing worse than finding out at the end of a project that there is little to no profit margin and there is nothing you can do about it.
Job costing is the key driver to grow your company.
By putting in a little extra effort upfront in planning how your organization tracks costs and utilizing the current technology solutions out there, construction businesses can understand where every dollar goes or has gone. This alone is massively important for keeping safe margins, and ensuring your team has the right tools to mitigate any potential disaster well before it comes to fruition
If you enjoyed this article, join our mailing list down below to see more content and stay up to date on what Ontraccr is developing to help digitize the construction industry.