Today, thankfully, prefabrication projects no longer require whole houses to be disassembled and then shipped across the ocean. Instead, individual components are manufactured in factories before being transported to the final construction site for assembly.
Modular Construction Versus Panelization
The term “modular construction” often pops up when talking about prefabrication, but what’s the difference?
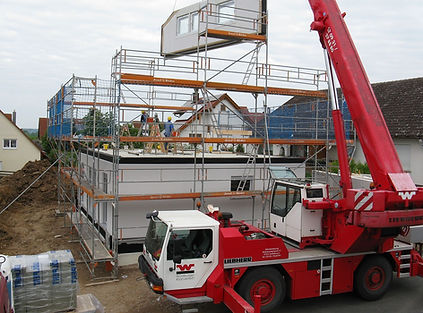
Simply put, modular construction is a type of prefabricated construction where entire sections of a building (including plumbing and electrical wiring) are put together before being transported to the construction site. This type of prefabricated construction requires the least amount of time on site, but a significant amount of planning to ensure all goes smoothly.
Panelization is another type of prefabricated construction where elements of a structure, such as walls or floors, are constructed in a factory and are then transported to an existing structure for installation (plumbing and electrical wiring are installed on-site).
Benefits of Prefabrication
Since the materials are stored in the factory, they are never exposed to the weather or elements before they reach the construction site; there’s no water, wind, or ice damage to worry about, and there are no construction delays due to inclement weather. With the components of the building being built in a factory, there’s less environmental degradation and noise pollution within the project’s surrounding environment.
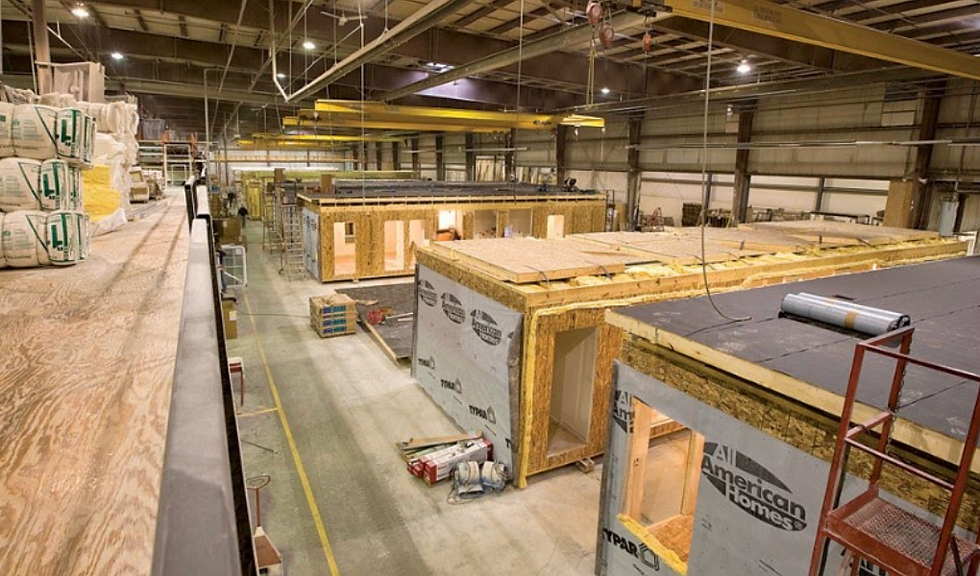
Since entire rooms (complete with plumbing and electrical systems) can be manufactured en masse in factories, prefabrication is particularly useful for projects with a high degree of repetitive designs: student dorms and hospital rooms, for example.
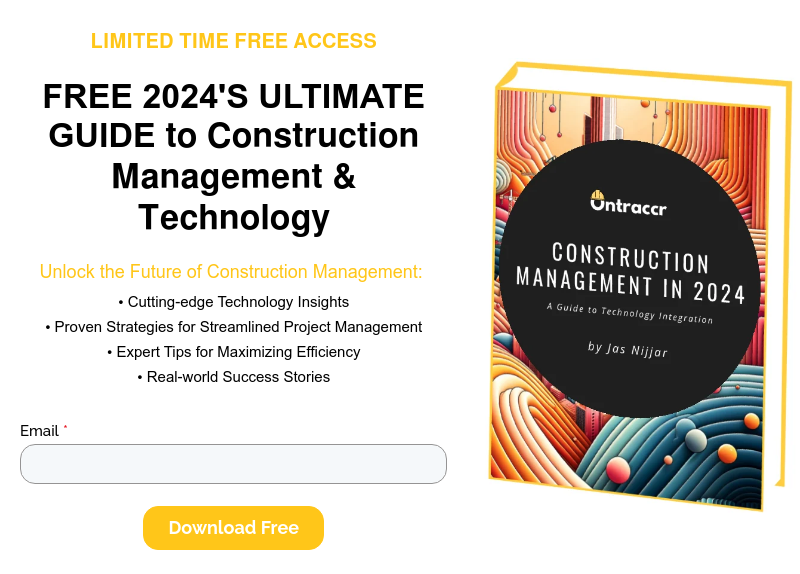
Prefabricated buildings aren't just limited to structures featuring accommodations as garages, barns, and offices have all been put up by various firms. Prefabrication also isn’t limited to low-rise projects, either; a pair of 56 storey skyscrapers dubbed Avenue South Residences are set to be put up in Singapore by the first quarter of 2023.
Due to the minimal time and number of workers needed on the work site, there’s the potential for big savings with prefabrication projects that can be put towards using high quality materials. (Note: Not all prefabricated materials are created equal! Durability and quality of finishes can vary widely depending on price.)
Costs for prefabrication homes can run between $200 and $250 CAD per square foot depending on the quality of finishes, though this will depend on location, with cities such as Vancouver and Toronto demanding higher prices than cities such as Halifax and St. John’s. Additionally, with less people expressing interest in joining skilled trades and thousands of workers set to retire soon, prefabricated materials can help alleviate some of the manpower shortage the construction industry currently faces.
Disadvantages of Prefabrication
For potential homeowners looking to save costs when constructing their homes, prefabrication can seem like an obvious choice, but there are some drawbacks that can affect them.
First, homeowners will have to first purchase the land they want to build on. Land doesn’t come cheap, and they will also have to pay for tree and plant removal, gravel, the costs of hooking up to utilities, etc..
Second, depending on where the home is planned to be put up, transportation fees can easily add up, particularly in those out-of-the-way areas.
Lastly, equally risky for both a buyer’s wallet and contractor’s reputation, components may be damaged during transport or assembly if the contractor lacks the proper equipment and experience working with prefabricated materials.
Closing Remarks
And there you have it: prefabrication in a nutshell. As time goes on and factories become quicker at turning out quality modules and panels, who knows what we’ll be able to achieve in terms of design and efficiency?
When paired with CWA automation software, contractors specializing in prefabrication can also increase efficiencies and quality control to ensure that this technology continues to advance. Exciting times are just around the corner!
If you enjoyed this article, join our mailing list now to receive all the latest articles and stay up-to-date on what OnTraccr is developing to bring automation to the construction industry!